What Are Direct to Film Transfers and How Do They Revolutionize Custom Printing?
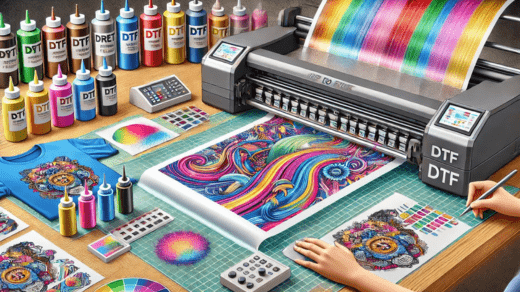
In the ever-evolving world of garment printing, new technologies continue to emerge, offering businesses and individuals more efficient, versatile, and high-quality printing solutions. One of the most exciting innovations in recent years is Direct to Film (DTF) transfers. As the demand for personalized, custom designs on clothing and other fabric-based products grows, DTF transfers have quickly become a game-changer in the custom printing industry.
This article will delve into what Direct to Film transfers are, how they work, the benefits they offer, and why they are revolutionizing custom printing. Whether you are a small business owner, a print shop operator, or an artist interested in custom apparel, understanding the power of DTF technology could transform your approach to printing.
What Are Direct to Film Transfers?
Direct to Film (DTF) transfers are a relatively new printing method that allows designs to be printed onto a special film and then transferred directly onto fabrics using a heat press. Unlike traditional methods like screen printing or direct-to-garment (DTG) printing, DTF transfers offer a more streamlined, versatile, and cost-effective way to print high-quality images on a wide variety of materials.
The process involves several steps:
- Printing the design: The design is printed onto a special transfer film using a DTF printer equipped with specialized inks. These inks are usually water-based pigment inks, which offer vibrant colors and strong durability.
- Applying adhesive powder: After printing, an adhesive powder is applied to the design on the film. This powder acts as a bonding agent that allows the design to adhere to the fabric when heat is applied.
- Curing the design: The adhesive powder and printed design are then cured by heating the film, ensuring the adhesive is ready to bond with the fabric.
- Heat pressing: The cured film is placed on the fabric, and a heat press is used to transfer the design onto the garment. The combination of heat and pressure activates the adhesive, allowing the design to fuse with the fabric.
- Peeling the film: Once the heat press process is complete, the transfer film is peeled away, leaving the vibrant design firmly embedded in the fabric.
How Direct to Film Transfers Work
One of the key advantages of DTF transfers is their simplicity and efficiency. Unlike DTG printing, which requires pre-treatment of garments and specialized equipment, DTF printing allows designs to be printed onto a film, which can be applied to any type of fabric or surface. This includes cotton, polyester, nylon, and even leather.
The DTF process can be broken down into three main stages:
- Design Creation: The process starts with the creation of the design. Graphic designers or artists can use software such as Adobe Illustrator or Photoshop to create a high-quality, detailed design. The designs are typically saved in formats like PNG or TIFF to preserve image quality.
- Film Printing: Once the design is ready, it is printed onto the special transfer film using a DTF printer. The printer uses a unique white ink layer in addition to colored inks, which ensures that the design remains vibrant and opaque, even on dark fabrics.
- Transfer Application: After printing, the film is heat pressed onto the fabric, transferring the design seamlessly. This step is quick and efficient, making it ideal for bulk production runs.
Benefits of Direct to Film Transfers
Direct to Film transfers are not only efficient and easy to use but also offer a range of benefits that set them apart from traditional printing methods. Here’s how DTF transfers revolutionize custom printing:
1. Versatility Across Different Fabrics
One of the most significant advantages of DTF transfers is their ability to work on almost any fabric. While traditional screen printing is often limited to cotton or cotton blends, and DTG printing struggles with non-cotton fabrics like polyester, DTF transfers can be applied to cotton, polyester, nylon, rayon, silk, denim, and even leather.
This versatility opens up new opportunities for custom printers who want to offer a wider range of products. Whether it’s t-shirts, hats, hoodies, or bags, DTF transfers can handle it all with ease.
2. Vibrant Colors and High Detail
DTF transfers allow for incredibly detailed and vibrant designs, even when printed on dark fabrics. The use of white ink in the printing process ensures that colors remain bright and vivid, regardless of the background color of the fabric. This makes DTF transfers an excellent choice for intricate designs, gradients, and multi-colored logos.
In addition, the fine resolution of DTF printers enables high-detail printing, making it possible to reproduce complex designs, artwork, and photographs with precision. Whether you’re creating a simple logo or a highly detailed artwork, DTF can handle it.
3. Durability and Longevity
Durability is another major advantage of Direct to Film transfers. Once applied, DTF transfers are highly resistant to wear and tear. They can withstand repeated washing, stretching, and general use without cracking, fading, or peeling. This durability makes DTF an ideal option for workwear, sports apparel, and other items that will undergo heavy use.
The adhesive powder used in DTF transfers creates a strong bond with the fabric, ensuring that the design remains intact for the life of the garment. As a result, customers are likely to be more satisfied with the longevity of their custom apparel, which can lead to repeat business.
4. Cost-Effectiveness for Small and Large Orders
Compared to other printing methods like screen printing, which requires setting up multiple screens for each color in the design, DTF transfers offer a cost-effective solution for both small and large orders. There’s no need to create screens, and the process itself is more streamlined, reducing setup times and labor costs.
For businesses that deal with custom or on-demand printing, this is especially important. DTF transfers allow for quick, affordable production without the limitations that come with minimum order quantities. Whether you’re printing one shirt or a hundred, the process is efficient and cost-effective.
5. Environmentally Friendly Option
In today’s market, sustainability is a growing concern for both businesses and consumers. DTF transfers are an environmentally friendly option because they reduce waste compared to other printing methods. For example, screen printing often involves excess ink, water, and chemicals, which can be harmful to the environment.
DTF transfers, on the other hand, use less ink, and the adhesive powder application process is more efficient, minimizing waste. Additionally, many DTF printing companies are now offering eco-friendly inks and films, further reducing the environmental impact.
6. No Need for Pre-Treatment
Unlike Direct to Garment (DTG) printing, which often requires the garment to be pre-treated with a special solution to make the fabric suitable for printing, DTF transfers do not require any pre-treatment. This eliminates an additional step in the production process, saving time and reducing the overall cost of printing.
The lack of pre-treatment also means that the DTF process can be used on a wider range of materials, as there are no compatibility issues with the chemicals involved in pre-treatment.
7. Efficient and Scalable for Businesses
DTF transfers are incredibly scalable, making them suitable for both small businesses and larger operations. Because the process is so streamlined, it’s easy to fulfill small, custom orders, while still maintaining the ability to handle large, bulk orders efficiently.
For print shops, this scalability is a major advantage as it allows them to grow their business without having to invest in significantly different processes or equipment. DTF transfers offer an affordable entry point for new businesses while also supporting the needs of established companies.
Why DTF Transfers Are Revolutionizing Custom Printing
Direct to Film transfers are not just another printing method—they represent a major leap forward in terms of flexibility, quality, and cost-efficiency in custom printing. The ability to print vibrant, durable designs on almost any type of fabric, combined with the cost-effectiveness of the process, makes DTF transfers an appealing option for businesses of all sizes.
For those looking to offer custom garment printing or expand their product offerings, DTF transfers provide the perfect balance of quality and efficiency. Whether you’re creating unique custom apparel for individual clients or producing large batches of promotional products, DTF transfers give you the freedom and flexibility to bring your designs to life with ease.
As more businesses and print shops adopt DTF technology, it’s clear that this method is set to become a staple in the world of custom printing, offering a revolution in how we think about printing on fabric.